PI(S):
Sponsor(s):
The device uses active magnetic bearings in combination with squeeze film dampers to form a very stable, vibration resistant motion control stage. Total travel is within a cube of 100 microns, and resolution in the linear axes is better than 0.5 nm. One possible application involves providing the sample motions required in scanned probe microscopy.
The Angstrom Stage is a six degree of freedom positioning stage for fine motion control. The stage ac
hieves a 6-sigmapositioning noise of 0.3 nm at 1 Hz measuring bandwidth and a controller bandwidth of 5 Hz. Total travel is within a cube of 100 microns. The single moving element is immersed in oil, forming squeeze film dampers between itself and the frame. This design results in a highly overdamped and vibration resistant system. Twel
ve electromagnets provide the forces necessary to suspend and servo the platen while six capacitance probes sense the position. All of the control algorithms are performed digitally, using a PC-based digital signal processing
board. The controller performs two functions that are essential to achieving 0.1 nanometer positioning resolution. First, it uses a detailed model of the stage in a feedback linearization scheme that linearizes and decouples the degrees of freedom. Second, it uses a combination of a digital filter and an estimator to reduce the effect of measurement noise by about two orders of magnitude. The end result is a stage that is suitable for positioning a sample with better than atomic resolution. Envisioned applications of the stage include producing the scanning motions required in scanned probe microscopy or as a motion control stage for integrated circuit metrology.
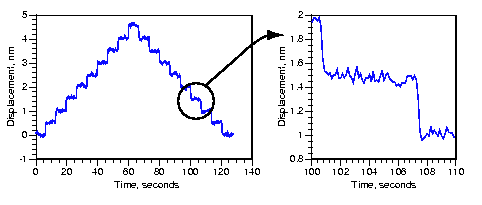